- Home
- /
- Design of Extruded Endless...
Design of Extruded Endless Splices
When designing endless splices for extruded profiles, several factors must be considered: durometer of compound, cut length, size of cross section and in the case of tubing, wall thickness.
Mold cavities are normally designed to the nominal dimension. If the extrudate cross section is at the top of the extruded tolerance, mold pressure marks will be visible on the surface and more so with the use of lower durometer compounds. If the extrudate cross section is at the low end of the extruded tolerance, the mold cavity would have to be shimmed in order to attain splicing pressure creating some surface marking. The longer the cut length, the greater the difference in size at each end. (One end may be on high tolerance and the other end on low tolerance.) Generally, this gives the appearance of a step or mismatch. See Figure 1.
Tubing is subject to the same considerations but in addition, thin wall tubing may require internal support in order to achieve sufficient molding pressure. The type of insert used and whether or not it should be removed would have to be resolved between manufacturer and purchaser.
It is to the advantage of both customer and rubber manufacturer to discuss design and application of extruded endless splices. See Figure 2.
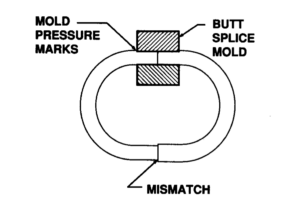
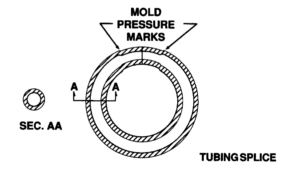
Please reach out to the COR Manufacturing team for additional details or information.